Case Study
Increasing the quality, efficiency and productivity of wood pellet production
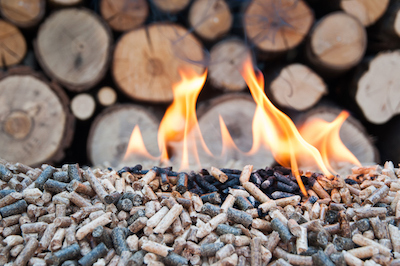
Problem
Automation of the wood pellet production, which involves heavy-duty woodcutters and clippers, would ensure consistency of the finished product and also reduce energy costs.
Solution
Optidrive P2 and E3s were introduced to control each section of the production process, from initial cutting to clipping and grinding stages. Twenty-five drives were commissioned in total, creating a 50 per cent reduction in energy costs and and increase of 65 per cent in productivity.
Nizamis S.A
A manufacturer of wood pellets and briquettes used for domestic and commercial fuel was finding consistent inconsistencies in the quality of its products during production due to the manual process involved.
Greece-based Nizamis S.A. wanted to automate production to ensure consistency, while also reducing costs through improved quality and energy efficiencies.
Invertek Drives variable frequency drives (VFD) were the perfect solution.
The process of manufacturing wood pellets from delivery and break down of the raw timber, through to the production of the pellets or briquettes, consists of a range of processes, with many using heavy-duty motors.
The raw material can be anything from crop waste and wood shavings to larger logs and tree branches.
The process uses heavy-duty woodcutters and clippers, through to sieves, grinders, pelletizing and air coolers. All elements of the process use a range of motors with varying demands and requirements.
Optidrive P2 is designed for industrial situations
Invertek Drives Optidrive P2 and Optidrive E3 were ideal solutions. The P2 is designed for industrial situations where heavy-duty processes are involved. This was needed in the initial cutting, clipping and grinding stages.
“The company’s workforce was manually handling the production of the raw product which meant there was inconsistency in its quality. This often resulted in the product needing to go through the process again and again, increasing costs,” said Theodore Amiridis of Automation Experts, Invertek Drives distributor in Greece.
Automation would ensure consistency and reduce costs
“They wanted to automate the system to ensure consistency while increasing efficiency and reducing energy costs.”
The E3 was used for the process elements of the process, including conveyors and lifts.
Both drives can be quickly installed and commissioned and provide precise motor control and energy savings within minutes of operation.
The drives were connected by ModBus communication which is standard on all of the drives.
“We installed and commissioned 25 drives and this immediately produced electrical savings of 50 per cent, in addition to increasing productivity by 65 per cent as well,” added Theodore. “The drives also ensured consistency throughout the process, with precise control over every motor.
Complete and efficient automotive production line
“The company now has a complete and efficient automotive production line.”
Dimitris Vrontelis of Nizamis S.A. said: “The drives have proved to be the best product for our production. They have ensured increases in efficiency and productivity which is a perfect solution for us.”
Rhydian Welson, Sales and Marketing Director at Invertek Drives, said: “Every application is different and that’s where Invertek’s variable frequency drives are ideal.
"They can be quickly and efficiently installed and commissioned with the parameters easily set for each process. Whether that’s using the pre-installed application modes on each drive, or where specific parameters are required.
“The increase in productivity and efficiencies Nizamis S.A. has more than returned the company’s investment in the automation of production using our drives.”