Using Closed Loop Control
Article 28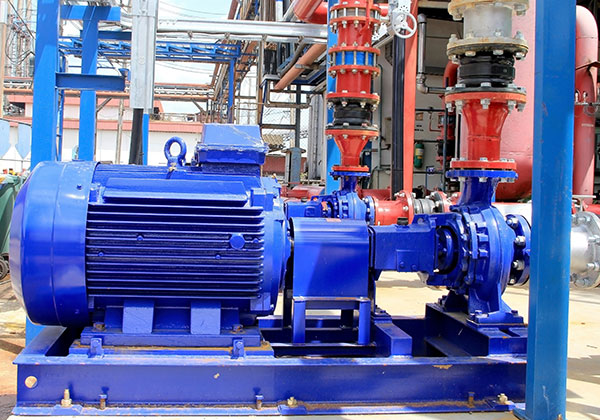
In an earlier article we described the basic principle of closed loop control. In this one, we’ll look more closely at some of the applications as well as problems that can be encountered.
First, let’s restate the basics of Closed Loop Control. In an open loop system, we hope that the speed of our motor will give us the result we want. If we are running a pump, we’ll hope that the flow rate, or pressure, or flow of coolant or whatever will be adequate. Of course, this means we have no control when things change, so we tend to oversize this solution, which can mean considerable waste of energy and money.
In a closed loop system, we fit a sensor to measure what we want to control, whether it is pressure, temperature, tension or speed etc. We connect the sensor back to the drive (this closes the loop) and the drive compares the actual value from the sensor with the desired value – the setpoint. The setpoint can come from an input (an analogue or serial input for example) or maybe it’s just a fixed value set in the drive.
The drive then adjusts the speed of the motor to try to minimise the error – the difference between the setpoint and the actual value from the sensor. There are various parameters in the drive to help stabilise the closed loop system. Adjusting the Proportional (P gain) Integral (I integrated value) or occasionally the Differential (D term) can stabilise a system that is oscillating or unresponsive.
So where is closed loop control used? Well, the obvious applications are to control pumps or fans. Many pumping systems need to maintain constant pressure (think of the hot water in a hotel in the morning, when everyone wants a shower) or flow rate. Fans may also be controlled by monitoring system pressure, but more usually temperature, or even Carbon Dioxide levels will be monitored and maintained. High levels of Carbon Dioxide tend to make people a bit sleepy - not desirable in offices and schools. These are great applications for closed loop control, but in many installations there are complex ducting systems, several fans and many sensors, so a central building management system tends to be used to maintain the temperature and air quality. However, there are plenty of simple applications where the drive’s built in closed loop controller can prove useful. As pumps and fans account for about half of all variable frequency drive sales, they account for at least half of the closed loop control applications.
Pressure control can also be used to maintain a constant vacuum. Many vacuum pumps have relatively crude controllers that simply vent into the system if the vacuum is too high. Replacing the vent with a vacuum sensor and use a closed loop drive saves lots of energy and money. A good example of this is in milking parlours, where the vacuum is used to milk the cows – better control is more comfortable for the cows as well!
So, where else can closed loop control be used? Tension control using a dancer arm has already been discussed in Article 9. Tension control can also be achieved using Torque Control, and torque control is another form of closed loop control; in this case, the drive monitors the load current and adjusts the output frequency to keep it constant. Article 15 describes torque control.
You might maintain the humidity in a greenhouse by controlling the supply of water mist, or you might want to reduce humidity by controlling an extractor fan in a laundry. In the case of the laundry, the difference between running the extractor at full speed all the time, and maintaining an acceptable level of humidity may represent a considerable cost saving.
Another application for closed loop control can be an indirect control of a process. In this case, we control the supply of material to a larger, often fixed speed process. An example is shown in Figure 1.
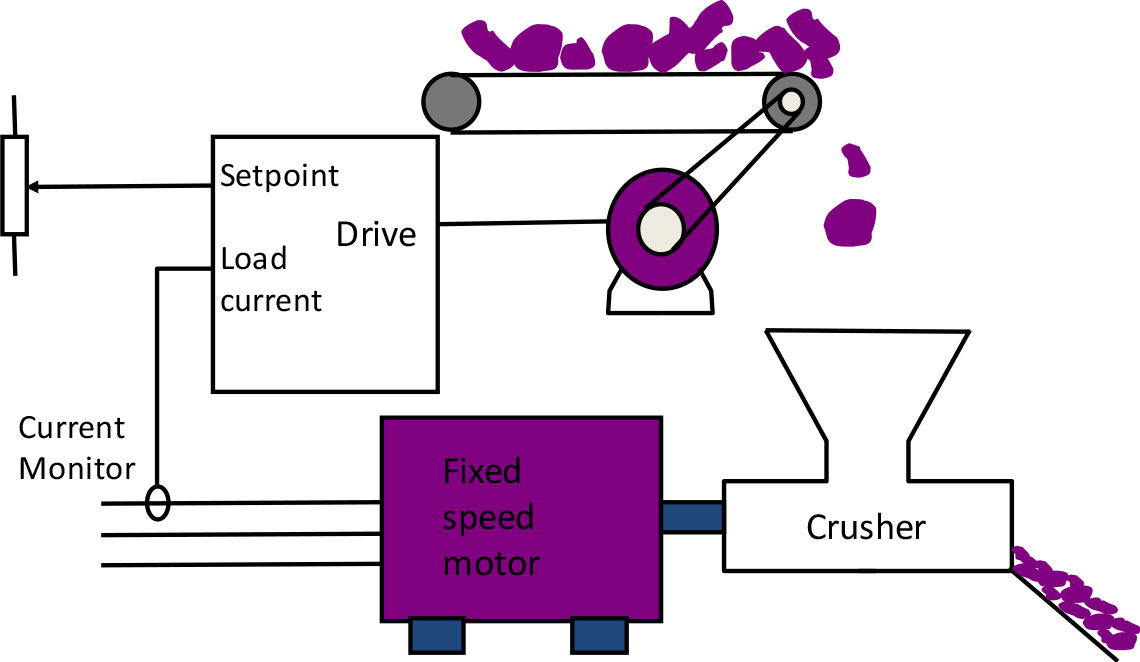
The large machine is crushing stone and is running at fixed speed. The stone is fed to the crusher by a conveyer, driven by a motor, controlled by a variable frequency drive. Now the stone that comes down the conveyer is varying in quantity, so the load on the main motor varies depending on the amount of material it receives. We can measure the load pretty well using a simple current monitor on the input of the fixed speed motor. Now, using closed loop control on the conveyer motor, we can speed up the conveyer if the load on the main motor is low, or slow it down if the motor load is high.
This seems a relatively simple application, but has been used in many different applications (such as wood powder manufacture, sugar cane crushing etc.) and, because the crusher is now running at maximum load setting all the time, the throughput is greatly increased, so the drive pays for itself in a matter of months.
So there are plenty of ways to use closed loop control besides maintaining temperature, pressure etc.
Encoders are a special case of closed loop control, and are described in article 17, Cranes Hoists and Elevators. The speed feedback from the encoder, usually mounted on the back of the motor, is fed to special inputs which allow the drive to measure the speed, direction of rotation, and sometimes the position of the motor shaft. But the same care needs to be taken as with any closed loop system. Is the signal from the encoder correct and indicating the expected speed? Is the system stable? Encoders are used in many applications where accurate speed holding is necessary, but are of particular importance in crane and elevator applications, where it is important to know exactly what is happening to the load when the brake is released.
Invertek have recently developed a modified closed loop control for use where the drive is fed from solar panels. The trick here is to get the maximum power from the panels by maintaining the voltage from the panels at their optimum operating point. Again, simple control gets significantly more power from the panels, improving the operation of the application, usually a remote irrigation pump.
Don’t be afraid of ‘closing the loop’ in a simple application. Article 9 describes in detail how to connect up and set up the system. As a result, you’ll have better control and probably save money and energy.